Source: Compiled by Future Think Tank from CITIC Securities' "Semiconductor Optics Theme Report: The cornerstone of semiconductor equipment, the future prospects of domestically produced ultra precision optics"
The "pearl in the palm of the eye" of the optical industry, with vast space for domestic substitution
The "pearl in the palm of the eye" of the optical industry tests manufacturers' ability to combine manufacturing
The manufacturing difficulty of industrial grade precision optical components is high, and they are key supporting components applied in high-tech industries. According to the definition in the prospectus of Maolai Optics, we can divide optical components into traditional optical components and precision optical components based on their accuracy and purpose. Among them, precision optical components can be further subdivided into consumer grade precision optical components and industrial grade precision optical components according to their application fields. Industrial grade precision optical components are mainly used in high-tech industries such as industrial measurement, semiconductor, life sciences, unmanned driving, biometric recognition, AR/VR detection, etc. They have strict requirements for process parameters, technical performance, application environment, and functional effects, which puts higher demands on manufacturing.
The ultra precision optical component processing technology tests the ability to combine manufacturing and system simulation. To produce optical components with high surface precision, high smoothness, and low reflectivity, manufacturers need to have excellent technical capabilities in optical design, material selection, processing technology, and post-processing. Optical design requires translating customer requirements into the geometric shape and optical properties of optical components, and selecting suitable materials based on design requirements. During the processing and post-processing, manufacturers need to convert design requirements into processing and surface treatment operations in order to achieve technical parameters such as surface shape accuracy, surface smoothness, and reflectivity. On the basis of existing manufacturing technologies such as polishing, coating, bonding, and active alignment, according to the information on the Zeiss official website, ultra precision optical processing also requires computer technologies such as complex instrument system design and simulation, high-end lens optimization design and simulation analysis, automatic control and signal acquisition system design and rapid implementation, image morphology/fusion/super-resolution/frequency domain processing, etc., in order to achieve the design and manufacturing of ultra precision optical components and systems.
There is a vast space for domestic substitution, and domestic manufacturers are making efforts in the field of ultra precision optics
Domestic ultra precision optical manufacturers rely on imported equipment, which is not conducive to the long-term improvement of their processing capabilities. For a long time, China's ultra precision optical industry has relied heavily on imported key manufacturing and testing equipment, and the reliability of domestically produced related equipment has been relatively low. According to the Reply to the Examination and Inquiry Letter on the Application Documents for Nanjing Maolai Optical Technology Co., Ltd.'s IPO and IPO on the Science and Technology Innovation Board, the key imported equipment used by Maolai Optical in the production process includes coating machines, interferometers, polishers, grinders, measuring instruments, etc. The main source countries and regions include Germany, the United States, Japan, the United Kingdom, Singapore, South Korea, Malaysia, Thailand, Hong Kong, China and Taiwan, China. Although the vast majority of manufacturing and testing equipment already have domestic alternative suppliers, there is currently no domestic alternative for some coating machines and magnetorheological polishing machine equipment. In the short term, the fulfillment of imported equipment orders is relatively smooth, and domestic ultra precision optical manufacturers can use imported equipment for process research and development production. In the long run, if domestic manufacturers gradually enter the high-end optical field and international trade frictions escalate, if China cannot form independent and controllable key manufacturing and testing equipment, or if it affects the development of optical systems in domestic semiconductor and life science fields.
There is still a significant gap between domestically produced ultra precision optical processing equipment and overseas counterparts. The ultra precision manufacturing technology and equipment for high-end optical components in China have a stage gap compared to the international forefront, which has become a major shortcoming restricting the development of the high-end equipment manufacturing industry. According to "Research on the Development of Ultra Precision Processing Technology and Equipment for High end Optical Components (2023)" (authors: Jiang Zhuangde, Li Changsheng, Sun Lin, etc.), the foundation of ultra precision optical component manufacturing is high-end optical processing machine tools. Although China has initially formed its own research and development capabilities for ultra precision processing machine tools, and the product varieties basically meet the needs of key fields, judging from the status after the implementation of the 04 special project, there is still a gap of about 15 years between China's machine tool industry and the international advanced level. Domestic optical manufacturers mainly rely on imported ultra precision optical processing, testing equipment, and core components.
A group of enterprises with great potential in key equipment and processing fields have been cultivated domestically, and China is expected to gradually achieve independent and controllable ultra precision optical components. At present, high-end equipment including basic equipment for manufacturing optical components with a diameter of 4m or more, lightweight and ultra precision grinding equipment, sub nanometer processing equipment, and ultra precision measuring instruments for ultra large aperture optical components are under foreign embargo. Domestic enterprises have grown into leading companies in the fields of consumer and industrial optical components, and are seeking breakthroughs in the field of ultra precision optical components. At present, a group of enterprises with a solid foundation in the field of high-end equipment have been cultivated in China, focusing on breakthroughs in common key technologies such as full spectrum nanometer/sub nanometer level precision creation, near defect free high surface integrity processing, forward design and data resource construction of ultra precision machine tools, and manufacturing of ultra precision intelligent machine tools. China is expected to gradually achieve independent and controllable production of domestically produced optical components for ultra precision optics.
The global industrial grade precision optics market is expected to reach 26.8 billion yuan by 2026
It is expected that the global market size of industrial grade precision optical components will reach 26.8 billion yuan by 2026. According to Frost&Sullivan data (cited from the prospectus of Maolai Optics), the global industrial grade precision optics market size is expected to reach 15.9 billion yuan in 2022, and is projected to reach 26.8 billion yuan in 2026, corresponding to a CAGR of 14% from 2022 to 2026. Benefiting from the rapid development of downstream fields such as life sciences, semiconductors, autonomous driving, biometric recognition, AR/VR detection, downstream customers have put forward higher requirements for precision optical systems, which is expected to promote the iteration of precision optical components towards industrial grade, and the scale of the industrial grade precision optical market is expected to continue to grow.
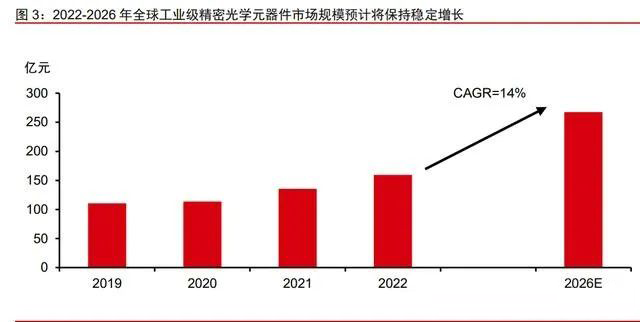
Semiconductor equipment and life sciences are important sub applications of global industrial precision optics. Benefiting from the rapid growth of scientific research and advanced manufacturing industries, as well as the continuous improvement of precision and lightweight requirements in the semiconductor and life sciences fields, we believe that the importance of industrial grade precision optical components is expected to continue to increase. According to Frost&Sullivan data (cited from the prospectus of Maolai Optics), in the field of life sciences, industrial grade precision optical products are mainly used in equipment such as gene sequencers and oral medical devices. It is expected that the market size will reach 5.3 billion yuan by 2026, corresponding to a CAGR of 11% from 2022 to 2026; In the semiconductor field, industrial grade precision optical products are mainly used in high-end equipment such as semiconductor testing and lithography machines. It is expected that the market size will reach 5.6 billion yuan by 2026, corresponding to a CAGR of 12% from 2022 to 2026.
Currently, German and Japanese manufacturers dominate the industrial precision optics market, while Chinese manufacturers held a 6% market share in the semiconductor market in 2021. With a long history of inheritance, a complete industrial chain system, and leading processing capabilities, Germany and Japan have a group of globally renowned optical component companies, including Zeiss, Nikon, Canon Jenoptik、 Leica, Olympus, etc. As the "pearl in the palm of the eye" of the optical components industry, the production of industrial grade precision optical components requires advanced manufacturing equipment and mastery of ultra precision optical processing technology. According to Frost&Sullivan data (cited from the prospectus of Maolai Optics), in 2021, Zeiss, Nikon, Canon Newport、Jenoptik、 International giants such as Leica and Olympus hold over 70% of the market share, with market shares in the semiconductor and life sciences fields reaching over 80% and 70% respectively. In recent years, with a large number of international precision optical enterprises setting up factories in China and establishing outsourcing relationships with domestic optical processing enterprises, domestic precision optical enterprises have seized the opportunity of industrial transfer, gradually narrowing the gap in technical level with international manufacturers in key links such as product design, manufacturing, and testing. According to Maolai Optics' calculations, their market share in the semiconductor and life science fields reached 6% and 12% respectively in 2021.
Throughout the entire semiconductor manufacturing process, precision optical systems serve as the 'industrial foundation'
Semiconductor processes continue to upgrade, with significant growth in manufacturing processes and investment
The advancement of semiconductor processes requires the development of higher integration density processes, and the difficulty of implementation continues to increase. For half a century, the growth rate of semiconductor device performance has followed the famous Moore's Law, and advanced semiconductor processes have evolved from planar structures to 3D structures. The transistor area has been continuously shrinking, and the number of transistors that integrated circuits can accommodate has maintained a pattern of doubling in about 18 months. According to the MKS Wanji Instrument Manual, we can see that the 3D NAND architecture stacks memory units to reduce overall space occupation; FinFET transistors are manufactured using 3D methods to reduce tunneling effects. With the improvement of semiconductor device integration, the industry needs to use more complex manufacturing processes, which puts forward higher requirements for materials and equipment.
The semiconductor process with nodes of 4nm and below has increased to nearly a thousand steps, and the yield rate of each step needs to exceed 99.99% to ensure an overall yield rate of 95%. According to Yole data (quoted from the "China Integrated Circuit Testing and Testing Industry Technology Innovation Roadmap" (Integrated Circuit Testing Instrument and Equipment Industry Technology Innovation Alliance)), for each generation of process node reduction, the number of fatal defects generated in the process will increase by 50%, and the yield rate of each process must be maintained at a very high level to ensure the final yield rate. According to the announcement from Zhongke Feice, there are hundreds of process steps for the 28nm process node. Due to the use of multi-layer etching technology, the process steps for nodes of 14nm and below have increased to nearly a thousand processes. When there are more than 500 processes, only by ensuring that the yield rate of each process exceeds 99.99%, can the final yield rate exceed 95%; When the yield rate of a single process drops to 99.98%, the final total yield rate will decrease to about 90%. Therefore, the challenge of process windows in the manufacturing process requires almost "zero defects".
The cost of advanced process chip assembly is rapidly increasing, and IBS data shows that the investment in 3nm process wafer equipment for every 50000 wafers will reach 21.5 billion yuan. Driven by Moore's Law, the significant increase in component integration requires the continuous reduction of integrated circuit line width, leading to increasingly complex production technology and manufacturing processes, and an exponential increase in manufacturing costs. According to IBS statistics (quoted from SMIC's prospectus), as technology nodes continue to shrink, equipment investment in integrated circuit manufacturing is showing a significant upward trend. Taking the 5nm technology node as an example, its investment cost is as high as 15.6 billion US dollars, which is more than twice that of 14nm and about four times that of 28nm. Therefore, the cost of chip fabrication in chip factories has also increased significantly. According to The Information Network data, the cost of 12nm process fabrication is approximately 3-5 million US dollars, while the cost of 5nm process fabrication is 40-50 million US dollars; The cost of using 2nm process for wafer fabrication is as high as 100 million US dollars.

The newly launched optical system runs through the entire semiconductor manufacturing process, with lithography and quantity/detection being important components of semiconductor equipment
Photolithography machines and semiconductor quantity/detection are important components of semiconductor equipment, and equipment upgrades drive technological progress. Semiconductor equipment has ten major categories of equipment, with lithography machines and measuring/testing equipment being important equipment for semiconductor manufacturing. According to Gartner data, lithography machines and semiconductor quantity/detection equipment account for 17% and 12% of the semiconductor equipment market, respectively. When technology nodes are upgraded to 5nm and below, there are significant changes in semiconductor manufacturing processes, and the further complexity of microstructure and manufacturing processes drives continuous upgrades of process equipment and quality control equipment. DUV lithography machines are limited by their wavelength, and their accuracy can no longer meet the process requirements. Wafer factories need to purchase more expensive EUV lithography machines or adopt multiple template processes, repeating multiple thin film deposition and etching processes to achieve smaller line widths, resulting in a significant increase in the number of thin film deposition and etching cycles, and higher requirements for yield control. Therefore, we believe that in the future, wafer fabs need to invest more and more advanced process equipment and yield control equipment.
Precision optical systems are an important component of lithography machines and measuring/testing equipment, covering the entire semiconductor manufacturing process. In the semiconductor manufacturing process, producing a qualified device requires hundreds of processing steps, each of which requires the use of relevant equipment for manufacturing and yield control. According to KLA (KeTian Semiconductor), semiconductor quantity/inspection basically covers the entire semiconductor manufacturing process, with optical inspection as the main principle of the quantity/inspection equipment. Each step must be perfectly executed to avoid the occurrence of fatal defects. In addition, for semiconductor devices, lithography is an important step in structure formation, and the lithography system, as a key component of the lithography machine, directly affects the process, speed, and yield. Therefore, we believe that precision optical systems have a significant impact on manufacturing processes and yield control, and are the core systems of semiconductor devices.
The optical system is an important component of lithography machines, and Zeiss is a global leader
The semiconductor industry's' crown ', lithography machines have been upgraded to EUV
The lithography machine is the core equipment for chip production, which directly affects the process nodes. Chip production mainly includes seven steps: deposition, photolithography, etching, etc. Among them, photolithography is the core step to achieve pattern transfer function: responsible for transferring the chip design pattern to the chip surface through optical development technology, and then manufacturing microstructures on the semiconductor wafer surface. The production of lithography machines has a high technological threshold, requiring highly precise physical equipment and strict control processes to achieve the required manufacturing accuracy. Advanced process technology requires advanced, high-resolution lithography machines for adaptation, as lithography machines directly affect the process and performance of chips.
Under the same manufacturing process, EUV can achieve cost reduction and efficiency improvement compared to DUV. EUV single unit price is relatively high, about twice the price of ArFi DUV. According to ASML's announcement, the current price of a single EUV device is approximately $150 million, while the price of an ArFi DUV is approximately $70 million. When the process advances to below 7nm, EUV lithography machines are introduced into semiconductor manufacturing and simplify some process steps, bringing significant improvements to semiconductor manufacturing costs and efficiency. If a DUV lithography machine is used, the wafer fab needs to use DUV for multiple exposures to complete the 7nm process pattern, while EUV only requires one exposure to complete. Reducing the number of exposures can reduce uncontrollable distortion, improve chip consistency and yield. According to TSMC data, the process for manufacturing 7nm chips using EUV for the first time is named N7+, which can increase circuit density by 15% -20% compared to the first generation N7 process; Under the same performance, power consumption can be reduced by 15%.
The optical system is the core component of the lithography machine, and the iteration of the lithography machine drives the upgrade of the optical system
The exposure system is the core of the lithography machine, and optical components are widely used in various lithography machine systems. According to the Chinese Academy of Engineering (quoted from Forward looking Industry Research Institute), an EUV lithography machine contains over 100000 components, mainly including lighting systems, workbench systems, exposure systems, etc., with over 5000 global suppliers. From the perspective of the structure of lithography machines, industrial grade ultra precision optical components are used in various subsystems of lithography machines. Various mirrors, lenses, and gratings constitute the complex optical system of lithography machines. Among them, the objective system is the core component of the lithography machine, which is related to the resolution and yield of the lithography machine.
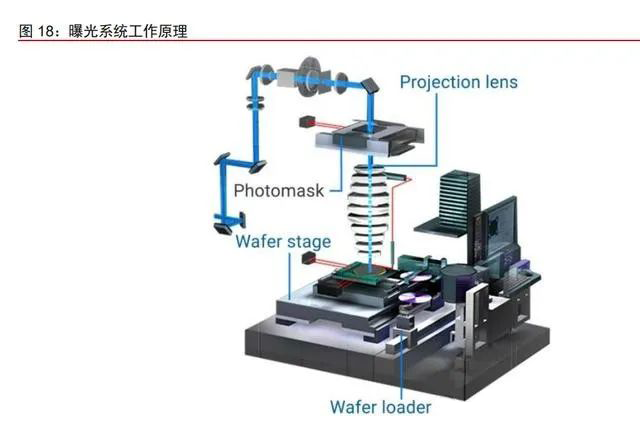
Looking back at the development history of lithography machines, the optical system has been continuously upgraded following the iteration of light sources. Since the birth of lithography machines, the light source has undergone six major upgrades, with the wavelength increased from 436nm to 13.5nm. As a global leader in ultra precision optics, Zeiss continues to introduce new optical systems to adapt to lithography machine upgrades. According to the Rayleigh formula, the development of lithography machines requires reducing the wavelength while increasing the numerical aperture. Upgrading the optical system is an important way for lithography machines to improve resolution, and together with the light source system, it affects the development of lithography technology. Before the development of EUV, the numerical aperture of optical systems continued to increase, resulting in a continuous increase in the number and volume of lenses in optical systems. With the development of lithography machines to EUV, the characteristic of 13.5nm EUV light being absorbed by lenses has also led to the optical system entering the era of "reflection", and the optical system remains one of the most important components of lithography machines.
The DUV optical system is a lens scheme, and ultraviolet fused silica or calcium fluoride (CaF2) is the material of the DUV transmission optical substrate. The projection objective lens needs to collect the first-order diffracted light emitted by the illumination module into the objective lens, then reduce the circuit pattern on the mask, focus the image on the wafer, and compensate for optical errors. Therefore, the projection objective lens is mainly composed of multiple lenses. Due to the typical transmittance curve of the material, which sharply decreases below 200nm, the DUV lens system requires the use of special materials such as UV fused silica or calcium fluoride (CaF2) coating. Meanwhile, polishing compounds and processes compatible with DUV wavelengths also need to be extensively researched and tested. Some polishing materials/compounds absorb UV/DUV light, which can affect the reliability and lifespan of optical components; Other materials may contain compounds that directly react with DUV light, causing system damage or malfunction. Precision optics has stricter requirements for surface polishing, and optical processing is completed using computer numerical control (CNC), magneto rheological calculation (MRF), oblique grinding (PL), and single point diamond turning (SPDT) processes.
The EUV optical system has been upgraded to a reflective system, and both the mask and objective systems are composed of special Bragg reflectors. EUV has a wavelength of 13.5nm, which is almost absorbed by all materials (including air). Therefore, EUV optical systems must operate under vacuum conditions, and the illumination system and projection objective system can transmit light from the intermediate focus to the light array using only reflective optical elements. Among them, the reflector is a Bragg reflector, which is a key system component that must have extremely low surface roughness (a few atoms) and high-precision flatness and curvature. The surface of EUV mirrors is coated with a Mo/Si multilayer film structure, with up to 100 layers stacked, achieving higher reflection efficiency through multilayer films. ZEISS and Fraunhofer IOF have jointly developed a unique coating system, which achieves a reflectivity of 70%. Due to the lack of optical materials that are transparent to EUV, the mask used in EUV lithography machines must also be reflective elements.
The value of optical systems will increase, and the market size of lithography machine optical systems will reach 6 billion US dollars by 2025
The iteration of the optical system has led to an 8-fold price difference between EUV lenses and DUV lenses. EUV optical systems are composed of special Bragg reflectors, with complex manufacturing processes and high prices. According to Edmund's information, EUV lenses have a higher unit price compared to DUV lenses, with an 8-fold price difference between EUV and DUV lenses of the same specifications. As advanced processes enter the 3nm era, EUV lithography machines have been widely used by leading wafer fabs. The next generation of High NA EUV lithography machines is expected to be launched in 2025, and EUV optical systems have become a trend or will enhance the importance of optical systems in lithography machines.
The ASML lithography machine contains over 100000 components, and the optical system suppliers mainly come from Germany. According to the Chinese Academy of Engineering (quoted from Forward looking Industry Research Institute), an EUV lithography machine contains over 100000 components and is supplied by more than 5000 global suppliers. From the structural analysis of the lithography machine, American light sources account for 27%, Dutch cavities and British vacuum systems account for 32%, Japanese materials account for 27%, and German optical systems account for 14%.
The EUV upgrade has driven the rapid growth of the lithography machine market, with a market size of 17.7 billion US dollars in 2022. The top three suppliers of lithography machines occupy the vast majority of the market share. From 2017 to 2022, the combined revenue of lithography machines from the three suppliers increased from $8 billion to $17.7 billion, corresponding to a CAGR of 17%. Looking ahead, according to ASML information, the proportion of the lithography machine market in the total semiconductor market has continued to increase in recent years, and this trend is expected to continue in the future. This is mainly due to the rapid development of the semiconductor industry in recent years, the expansion of advanced processes has led to a rise in capital expenditures for wafer fabs, and the increase in the proportion of equipment expenditures is expected to bring sustained growth to lithography machines, maintaining a rapid growth in market size.
The value of high-end lithography machine optical systems is high, and the global lithography machine optical system market is expected to reach $6 billion by 2025. With the development of advanced processes, the global shipment volume of EUV lithography machines continues to increase, and the next generation of High NA EUV is expected to be shipped in 2025. The market share of EUV lithography machines is expected to maintain growth. Due to the difficulty in manufacturing EUV optical systems, the value of EUV optical systems exclusively supplied by Zeiss Semiconductor Division far exceeds that of other types of lithography machine optical systems, and the importance of optical systems is increasing day by day. Based on our predictions of global lithography machine shipments, prices, and the proportion of optical system prices, we estimate that the global lithography machine optical system market is expected to reach $6 billion by 2025, corresponding to a CAGR of 25% from 2022 to 2025.
1) Assumption for global lithography machine shipments in 2025: According to ASML's forecast, the global semiconductor market will maintain stable growth from 2020 to 2030, with a CAGR of 9% during this period. The continued growth of the semiconductor industry will drive an increase in wafer demand, with advanced and mature processes expected to have a compound annual growth rate of 12% and 6% respectively. Wafer fabs need to expand production to meet the demand growth. Therefore, we assume that the market demand for EUV lithography machines used in advanced processes and ArF lithography machines used in auxiliary production will rapidly increase, and the shipment volume is expected to reach 80 and 280 units respectively by 2025.
2) Assuming the price of lithography machines in 2025: According to ASML data, the price of High NA EUV is expected to reach 350 million US dollars; By analyzing the prices of various types of ASML lithography machines from 2018 to 2022, except for EUV lithography machines, which maintained a slight increase in price, the prices of other models of lithography machines remained stable. We believe that the global lithography machine industry is an oligopolistic market with relatively small price fluctuations. It is expected that EUV lithography machine shipments will enter a small growth range from 2022 to 2025, and prices will remain stable. The prices of other types of lithography machines will continue to remain stable.
3) Assuming the proportion of optical systems in the price of lithography machines: Zeiss Semiconductor Division mainly produces ultra precision semiconductor optical systems, with ASML as its main customer. According to ASML and Zeiss announcements, 90% of the revenue of Zeiss Semiconductor Division from 2015 to 2022 comes from ASML, and Zeiss Semiconductor Division is the only supplier of ASML lithography machine optical systems. Therefore, by analyzing the revenue of Zeiss Semiconductor Business Unit and the shipment volume and average selling price of ASML lithography machines, we estimated the assumption of the proportion of various types of lithography machine optical systems to lithography machine selling prices.
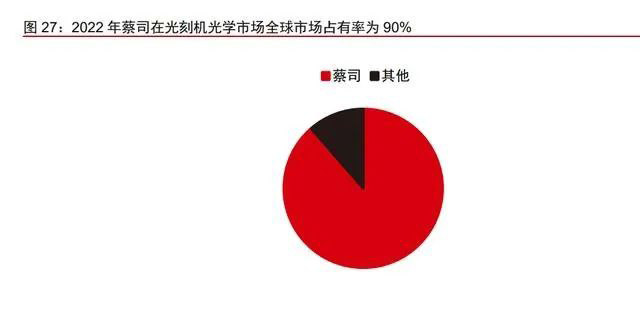
Domestic lithography machine optical systems have a long way to go, and Zeiss is the global leader in lithography machine optical systems
Zeiss is a global leader in lithography optical systems, with a market share of 90% by 2022. According to ASML's announcement, Zeiss is the main supplier of core optical systems for ASML lithography machines, especially the only supplier in the EUV lithography machine field. In 2016, ASML directly invested 1 billion euros to acquire a 24.9% stake in Zeiss SMT, a subsidiary of Zeiss Semiconductor, and reached a cooperation principle of "two companies, one business" with Zeiss Semiconductor to jointly promote the development of advanced lithography machines. Therefore, after ASML grew into an absolute leader in the lithography machine market, Zeiss also became a leading enterprise in lithography machine optical systems. Based on ASML and Zeiss' announcement, we estimate that Zeiss' global market share will reach 90% in 2022.
There is still a significant gap between the optical component parameters of domestic lithography machines and Zeiss, and the optical system of domestic lithography machines has a long way to go. China has accumulated rich technical experience in the field of optics and has a good technological foundation in consumer grade, laser, and optical communication fields. However, there is still a significant gap between China and the international first-class level in industrial grade ultra precision optics such as semiconductors. At present, Changchun Institute of Optics and Fine Mechanics is a leader in the field of ultra precision optics in China, and has made certain progress in DUV lens systems and EUV mirror systems. According to Zeiss ASML、 On the official websites of Guoke Precision and Changchun Institute of Optics and Fine Mechanics, the DUV lithography machine optical system launched by Guoke Precision can meet the 90nm process node, and there is still a gap of more than three generations compared to the Zeiss DUV optical system; However, there is still a significant gap between the surface accuracy of the EUV optical system developed by Changchun Institute of Optics and Fine Mechanics for the national science and technology major special project "Key Technology Research of Extreme Ultraviolet Lithography" and Zeiss. There is still a significant gap between China and overseas in the field of lithography machine optical systems, but in recent years, domestic enterprises and research institutes have increased their research and development efforts in semiconductor optics, and their technical capabilities are expected to improve rapidly.
The front-end optical detection equipment is the mainstream solution, and the optical system is an important support
Yield control is crucial for chip manufacturing, and inspection/measurement runs through the entire manufacturing process
The quality control of the front-end process and advanced packaging can be divided into inspection and metrology stages. Detection refers to the detection of heterogeneous conditions on the surface of a wafer or circuit structure, such as particle contamination, surface scratches, open and short circuits, and other characteristic structural defects that have adverse effects on chip process performance; Measurement refers to the quantitative description of the structural dimensions and material properties on the observed wafer circuit, such as the measurement of physical parameters such as film thickness, critical dimensions, etching depth, and surface morphology. According to different types of testing, semiconductor quality control equipment can be divided into testing equipment and measuring equipment.
The detection and measurement process runs through the entire pre process and advanced packaging process, and at least 7 types of measurement/detection equipment are required for processes such as photolithography and etching. Measurement/testing equipment is mainly used in front-end processes and advanced packaging, covering almost all sub processes, and is one of the key elements to ensure chip production yield. According to VLSI Research data, the sales proportion of detection equipment is relatively high, about 62.6%. Among them, the nano pattern wafer defect detection equipment has the highest sales proportion, with sales of 1.89 billion US dollars in 2020; The sales revenue of critical dimension measuring equipment accounts for the highest proportion among measuring devices, with a sales revenue of 780 million US dollars in 2020. In the specific processes of front-end and advanced packaging, photolithography, etching, and CMP have a high demand for detection and measurement equipment, requiring at least 7 different types of measurement/detection equipment.
Quantity/detection includes three major technological routes, with optical detection technology accounting for over 75% of the market share
Semiconductor quantity/detection includes technologies such as optical detection, electron beam detection, and X-ray quantity measurement. The differences between optical detection technology, electron beam detection technology, and X-ray light measurement technology include detection accuracy, detection speed, and application scenarios. Optical detection technology has more advantages in detection speed, and under the same conditions, the speed can be more than 1000 times faster than electron beam detection technology. Therefore, electron beam detection technology is mainly applied in scenarios with low throughput requirements, such as re examination of nanoscale defects, surface scale measurement of some key areas, and sampling of some key areas. Compared with X-ray measurement technology, optical detection technology has a wider range of applications, while X-ray measurement technology is mainly used in specific fields such as metal composition measurement and ultra-thin film measurement, with relatively narrow applicability scenarios.
The application of optical detection technology in equipment has a wide range of scenarios, with a market share of over 75% in 2020. Equipment utilizing optical detection technology can achieve a good balance between accuracy and speed, and can meet functions that other technologies cannot achieve, such as 3D morphology measurement, photolithography overlay measurement, and multi-layer film thickness measurement. According to VLSI Research and QY Research data, in the global semiconductor detection and measurement equipment market in 2020, the market share of devices using optical detection technology, electron beam detection technology, and X-ray light measurement technology was 75.2%, 18.7%, and 2.2%, respectively, with devices using optical detection technology accounting for the largest proportion.
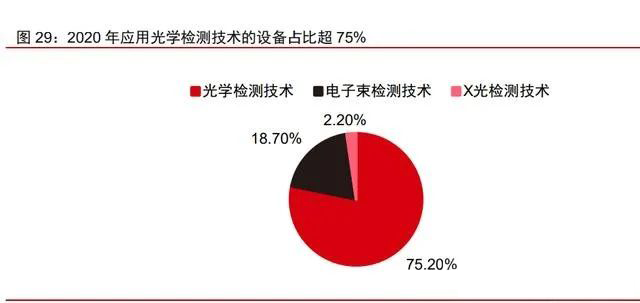
Optical detection technology is widely used in the measurement/detection process, with rich technical classifications. Semiconductor optical quantity/detection equipment has a wide range of applicable scenarios and is widely used in advanced semiconductor processes. In the detection process, optical detection technology can be further divided into non patterned wafer laser scanning detection technology, patterned wafer imaging detection technology, and photolithography mask plate imaging detection technology. In the measurement process, optical detection technology is based on the fluctuation and coherence of light to measure optical scales far smaller than wavelength. Measurement in integrated circuit manufacturing and advanced packaging mainly includes three-dimensional morphology measurement, thin film thickness measurement, etching accuracy measurement, critical dimension measurement, etc.
The resolution of semiconductor quantity/detection equipment continues to improve, and the market size of supporting optical systems is expected to reach 1.3 billion US dollars by 2024
The semiconductor process has evolved towards sub nanometer technology, driving the development of quantity/detection techniques. Top semiconductor manufacturers have upgraded their processes to 3nm technology, and new technologies such as 3D FinFET transistors and 3D NAND have become mainstream process technologies in the industry. In order to meet the development trend and requirements of detection and measurement technology towards high speed, high sensitivity, high accuracy, high repeatability, and high cost-effectiveness, the industry has made improvements by enhancing resolution, improving algorithm and software performance, and increasing device throughput, such as increasing the intensity of illumination, extending the spectral range to the DUV band, increasing the numerical aperture of optical systems, increasing the optical mode of illumination and acquisition, expanding the application of optical algorithms and optical simulation in the field of detection and measurement.
The optical system is an important component of semiconductor optical detection equipment and needs to meet high NA and low aberration requirements. The optical path design of semiconductor optical detection equipment is relatively complex and requires high quality of the optical system. Taking a typical bright field optical defect detection equipment as an example, the equipment uses a Kohler illumination path to modulate the high brightness and wide spectrum plasma light source beam into a super uniform, polarized beam with a specific beam cross-sectional shape; Afterwards, a high NA and low aberration objective lens system is used to collect scattered light caused by structural defects in silicon wafers. The scattered light is then imaged onto a Time Delay Integration (TDI) camera through an imaging path combining a refractive index hybrid lens group and a zoom lens group; Finally, the accurate recognition of defect signals is achieved using a slice to slice image differencing algorithm.
In the era of below 10nm process, semiconductor optical detection equipment needs to upgrade its light source to VUV light. At present, the high-end K39XX series and K29XX series bright field optical defect detection equipment developed by KLA in the United States can achieve a defect detection sensitivity of sub 30nm, and the yield can maintain 1WPH (Wafer Per Hour) @ 36nm, suitable for defect detection of silicon wafer structural patterns on 1Xnm and below node process production lines. In order to achieve advanced process sub nanometer level defect detection, the industry needs to design special optical path systems based on the reflection and transmission characteristics of semiconductor materials. According to KLA Workshop information, KLA adopts LSP light source technology to achieve nanoscale defect detection, where the optical system is similar to EUV lithography machines and requires the use of ultra precision optical processing mirrors for optical path design. Therefore, we believe that as the demand for nanoscale defect detection increases, equipment will need to use ultra precision optical processing technology to replace some lenses with mirrors, and the design of the optical system will become more complex. Overall, the value of the optical system is expected to increase.
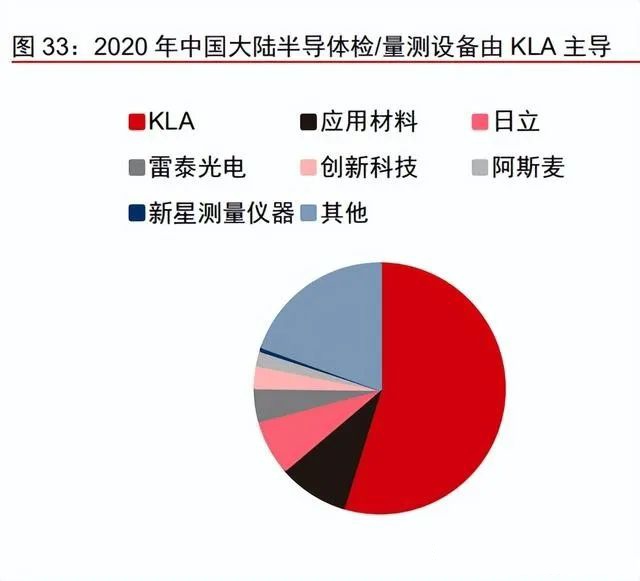
The value of semiconductor quantity/detection equipment optical systems has increased, and we expect the global semiconductor quantity/detection equipment optical system market size to reach $1.3 billion by 2024. With the development of advanced processes, process nodes below 10nm are rapidly advancing, and the semiconductor quantity/detection equipment required for advanced processes has high requirements for accuracy and throughput. Taking the global semiconductor quantity/testing equipment leader KLA as an example, in order to adapt to process node defects below 10nm, KLA has launched a wide spectrum DUV continuous laser optical detection system, which puts higher requirements on the optical system. Based on our predictions of factors such as the global semiconductor volume/testing equipment market size and the proportion of optical system value, we believe that the global semiconductor volume/testing equipment supporting optical system market size is expected to reach $1.3 billion by 2024.
1) Assumption for Global Semiconductor Volume/Testing Equipment Market Size in 2023-2024: With increasingly advanced processes and increasing number of process links, the volume/testing equipment market size is expected to steadily grow. According to data from the Huajing Industry Research Institute, the proportion of investment in wafer manufacturing equipment to testing equipment in 2021 is approximately 11%. According to Gartner and SEMI forecasts, the global wafer manufacturing equipment market is expected to reach $100 billion by 2024. In recent years, the main equipment required for semiconductor manufacturing has not undergone significant changes. We believe that the proportion of semiconductor volume/testing equipment in the semiconductor equipment market is expected to remain at 11%, and the global semiconductor volume/testing equipment market size is expected to be $12.5 billion by 2024.
2) Assumption for the Value Proportion of Supporting Optical Systems in 2024: According to Gartner data, the global semiconductor volume/testing equipment market will maintain stable growth from 2018 to 2022, with a market size of up to 13.5 billion US dollars in 2022. According to the prospectus of Zhongke Feice, from 2019 to 2021, the average annual cost of optical raw materials for Zhongke Feice's semiconductor quantity/testing equipment was 35.5% of the total procurement cost. Among them, optical components account for about 60% of optical raw materials, except for components such as laser light sources, cameras, lenses, and sensors. Based on the above data, we estimate that the optical system supporting the measuring/testing equipment accounts for approximately 10% of the equipment's value. At present, the domestic semiconductor production/testing equipment manufacturing level is in the middle of the industry, and the cost breakdown of equipment has reference value. We believe that the assumption of 10% is reasonable to some extent.
At the right time for domestic substitution of semiconductor quantity/detection equipment, there is a vast space for optical component substitution
The market share of KLA exceeds 50%, and the localization rate of equipment is expected to accelerate. According to VLSI Research and QY Research data, the global semiconductor inspection/measurement equipment market has a high concentration, with KLA holding over 50% of the global market share in 2020. Other inspection/measurement equipment manufacturers include Applied Materials, Hitachi, and Raytheon Optoelectronics. In 2020, the top five global manufacturers were all from the United States and Japan, accounting for over 82% of the market share; The domestic market is also monopolized by American and Japanese manufacturers, with the top five manufacturers holding over 78% of the market share. At present, the semiconductor industry chain in Chinese Mainland is in a period of rapid development, with major technological breakthroughs from upstream raw materials to end wafer foundry. The manufacturers of inspection/measurement equipment in Chinese Mainland have made some breakthroughs in manufacturing technology and product lines, and the localization rate is expected to accelerate in the future.
Domestic suppliers must have the supply capability, and Maolai Optical Semiconductor's revenue from testing optics is growing rapidly. In the field of semiconductor quantity/detection equipment, leading domestic optical manufacturers represented by Maolai Optics have initially acquired the ability to supply relevant optical modules to industry-leading customers. According to the prospectus of Maolai Optics, Maolai Optics has developed semiconductor detection optical modules for globally renowned semiconductor detection equipment manufacturers such as Camtek and KLA. However, the related market is still dominated by overseas optical manufacturers such as Newport, Zeiss, Zygo, and Jenoptik. We believe that the processing difficulty of semiconductor quantity/detection equipment optical systems is smaller than that of lithography machines. Domestic manufacturers are expected to quickly increase their market share after initially mastering the process. In 2019-22H1, Maolai Optical's semiconductor quantity/detection optical revenue maintained rapid growth, and in 2021, its revenue reached 80.52 million yuan.
Disclaimer: This article is reproduced or adapted online, and the copyright belongs to the original author. The content of the article is the author's personal opinion. Reproduction is only intended to convey a different viewpoint and does not represent the company's endorsement or support of that viewpoint. If you have any objections, please feel free to contact us.